Bij een in situ gestort dek wordt de oplegging op de betonpoer doorgaans gesteld voorafgaand aan het bekisten van het dek. Ook deze oplegging moet gesteld worden op een contactvlak met hoge eisen (zie hoofdstuk 6.3.3). Na het storten en verharden van het dek is het bovenvlak van de oplegging nog steeds waterpas maar is het gefixeerd in het verhardende beton. Afhankelijk van de bouwfasering treden na het ontkisten, na de eventuele 100% voorspanning en na het aanbrengen van het asfalt en overige rustende belastingen, hoekverdraaiingen en translaties op. Deze hoekverdraaiingen en translaties moeten meegenomen worden in het ontwerp van de oplegging (zie hoofdstuk 3).
Omdat rubber opleggingen vooraf niet in te stellen zijn, is het aan te bevelen om bij grote hoekverdraaiingen en translaties in de bouwfase deze in situ dekken te voorzien van dummy-opleggingen. Deze dummy-opleggingen moeten dan aan het eind van de bouw vervangen worden door de definitieve opleggingen. De definitieve oplegging kan dan gesteld worden met een bovensabeling.
Als gewerkt wordt met dummy- opleggingen moet altijd rekening worden gehouden met de compressie van de definitief belaste oplegging. Het dek dient dus hoger op zijn dummy opleggingen te liggen dan uiteindelijk gewenst. Deze compressie is redelijk onvoorspelbaar, dus ook de definitieve hoogte van het dek. Heel globaal kan worden aangehouden dat elke 30 mm rubberoplegging 1 mm compressie veroorzaakt. Vanwege dit fenomeen is het raadzaam de voegovergangen ook aan te brengen na het aanbrengen van de definitieve opleggingen.
Een voorbeeld van een veel toegepast bekistingsdetail is onderstaande figuur. Hierbij is in de vloerbekisting een sparing gezaagd gelijk aan de buitenzijde van de oplegging. Het bovenvlak van de oplegging is gelijk aan de bovenzijde van de bekistingplaat.
Figuur 6.3.4.a Bekistingsdetail rubber oplegging in situ rijdekBij uitvoering brengt deze methode de volgende risico’s met zich mee:
- De sparing in de bekisting is groter dan de oplegging zelf met als gevolg dat lekkage tijdens de stort optreedt. Cementwater en eventueel beton lopen dan langs de oplegging.
Een “vuile“ oplegging is nooit goed te inspecteren en als ook beton is weggelekt kan in de gebruiksfase de oplegging niet goed functioneren door belemmerde translatie.
Bovendien veroorzaakt wegsijpelend cementwater tijdens het stort grindnesten in het dek. Dit is ronduit zeer ongewenst omdat de krachten in het beton juist boven de opleggingen groot zijn. Lekkage is goed tegen te gaan door afkitten van de kist/oplegging met siliconen kit. - De bekisting gaat zich zetten tijdens de stort door het toenemende bovenliggende betongewicht. Het is onvermijdelijk dat knijp optreedt: in de baddingen, wiggen en de hulpondersteuning van de kist zelf. Vervolgens blijkt na ontkisten dat de oplegging deels is ingestort in het dek! Vervanging in de toekomst is dan uitsluitend met extra inspanning mogelijk. Er moet extra in hoogte gevijzeld worden waarbij de grote kans bestaat dat de bovenliggende voegovergang deze extra vijzelhoogte niet verdraagt (zie ook hoofdstuk 6.5.3). Daarnaast wordt het deels ingestorte rubberblok in zijn vervormingen beperkt. Deze ongewenste situatie is weergegeven in onderstaande figuur.
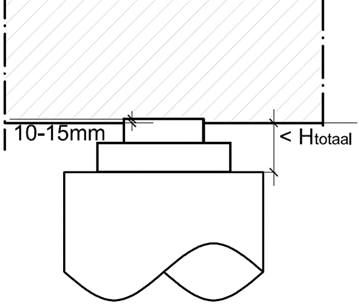
In verband met de hierboven genoemde risico’s is het beter om de oplegging halverwege het bovenvlak van de bekistingplaat te positioneren. Een groot nadelig gevolg hiervan is echter dan wel, dat het rubberbovenvlak verdiept in de bekisting komt te liggen, waarin vuil en vlechtdraad zich kan ophopen voorafgaand aan het storten. Ook wordt vrijwel altijd het bovenvlak van de oplegging zeer glad door ophopende bekistingsolie. Een dergelijke verdiepte ligging van het oplegblok is ook altijd aanwezig, als het dek zich in een lengte en/of een dwarsafschot bevindt. Zie ook onderstaand figuur.
Vlak dek: vuilbak! Sterk hellend dek 3D uitkisten: vuilbak!
Figuur 6.3.4.c Verdiepte positie van bovenkant rubber oplegging in bekistingDeze nadelen zijn te voorkomen door in het werk-/keuringsplan van de kist en stort van het dek expliciet op te nemen dat er geen bekistingolie direct op de opleggingen gespoten mag worden. Ook moeten deze “oplegging bakken” zeer zorgvuldig schoongemaakt worden met een controle aspect voor elke oplegging. Bij voorgespannen dekken, juist bij de landhoofden boven de opleggingen bevindt zich veel wapening. Deze wapening maakt het schoonmaken van de “oplegging bakken“ een lastig uitvoeringsaspect, maar is niet onmogelijk. Dit schoonmaken kost niet zoveel: alleen tijd en expliciete aandacht. Nog even ’s avonds laat de kist schoonspuiten, zonder zaklantaarn voor controle en de volgende morgenvroeg storten is dan vragen om grote problemen, welke pas te zien zijn na het ontkisten.
Stalen overgangsplaten
Om alle bovengenoemde uitvoering risico’s te beheersen kan ervoor gekozen worden de oplegging tussen twee staalplaten te stellen. Zie onderstaand figuur. De staalplaten altijd voorzien van doken/ankers om de plaats vastheid te waarborgen.
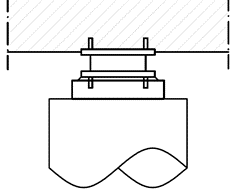
De volgende voordelen zijn aan te merken bij toepassing van rubberopleggingen tussen staalplaten:
- Het niet waterpas en/of vlak zijn van de in situ gestorte betonpoeren wordt gecompenseerd met een nauwkeurig op hoogte te stellen en te ondersabelen stalen onder plaat.
- Diktetoleranties in de oplegging kunnen worden opgevangen.
- Betrouwbare en constante wrijving tussen rubberblok en staalplaat (in het ontwerp dient dan wel de lage wrijvings- of k-factor van 0,2 te zijn aangehouden).
- De bovenzijde van de bovenste staalplaat (bijvoorbeeld 30 mm dik) bevindt zich in de stortfase hoger dan de kist (b.v. 10mm) , zodat er geen vuilophoping optreedt. Dit grote voordeel is dus juist van toepassing bij dekken met een hellende onderzijde. Dit hoeft dus ook niet duurder te zijn dan het 3D uitkisten van een houten vloerkist zoals bij het vorige figuur van het sterk hellende dek getoond.
- Het rubberblok is zeer goed te vervangen, doordat het niet ingestort is geraakt.
- Als de opleggingen tijdens het bouwproces een extreme translatie hebben ondergaan, welke groter is dan de translatie in de gebruiksfase, moet het dek opgevijzeld kunnen worden om de oplegging vrij te laten springen (zie hoofdstuk 6.4.6). Een grotere staalplaat (bijvoorbeeld rondom 50 mm.) geeft dan ook alle gelegenheid aan het blok voor deze verplaatsing. Na het afvijzelen draagt dan het blok weer egaal.
Zeker bij grote opleggingen (b.v. 500 bij 500 mm en groter) zijn de genoemde voordelen relevant. Een andere optie is het boven en ondergieten van de rubber oplegging (zie par. 6.3.6).
Als stalen overgangsplaten worden toegepast moeten deze overigens altijd voldoen aan de eisen:
- Ontwerp: Conform RTD 1012 (2017) art. 8.2:
- Belasting combinatie ULS.
- Mobiliseren schuifcapaciteit tussen oplegging en overgangsplaat resp. betonconstructie. Waarbij: Cap.= 0,5* V min *µ. In ieder geval dient de verbinding tenminste te bestaan uit 4 bouten M16 10.9.
- Voor verbindingen aan de hoofdconstructies geld dat in aanvulling op de ontworpen capaciteit een extra capaciteit van 30% van de horizontale ontwerpkracht d.m.v. ankers e/d/ moet kunnen worden overgedragen.
- Materiaal: Conform RTD 1012 (2017) art. 8.3 :
- Overgangsplaten dienen een vlakheid te hebben < 1/1000 van de diagonaal.
- De vlakheid, conservering en bevestigingen moeten worden gerapporteerd.
Het is noodzakelijk deze hoge eisen te bewaken om de volgende redenen:
- Een staalplaat heeft bij levering als onafgewerkt halffabricaat waarschijnlijk al een grotere afwijking dan de toegestane afwijking volgens de eis.
- Elke wijze van fabricage heeft zijn eigen wijze van warmte-inbreng en daarmee risico op vervorming. Onder fabricage wordt verstaan het totale proces: van levering materialen, eventuele bevestiging ankers aan de staalplaten tot conservering. In onderstaande tabel een overzicht.
Tabel 6.3.4.e Overzicht conserveringsmethoden overgangsplaten
Fabricage proces | Methode | Risico/ gevolg |
Formeren staalplaat |
|
|
Bevestiging doken/ankers
|
|
|
Conservering
(altijd conform RTD 1012 (2017) art. 7.9.1: ISO 12944, en art. 8.3)
|
|
|
Opmerking bij tabel: De plaats vastheid van rubber opleggingen op elke conservering kan absoluut worden gemaakt door het opsluiten van het rubberblok via uitwendige, opgebouwde stalen trippen of inwendige doken. Zie hiervoor hoofdstuk 6.3.9.
Bovenstaande uitvoeringsrisico’s dienen in het ontwerp met zijn werkvoorbereiding nadrukkelijk onderkend te worden. Deze kunnen praktisch worden beheerst op de volgende wijzen:
- Via na bewerken (vlak vrezen) van de staalplaten. De laatste stap conservering blijft dan nog wel aanvullend te beheersen.
- Zet de productie van de behandelde staalplaten zeer tijdig uit, opdat bij afkeur nog ruimte is voor herproductie.
Neem +/- 5 % van het aantal staalplaten extra in productie, zodat na controle er volume is voor afkeur, zonder planningsproblemen.